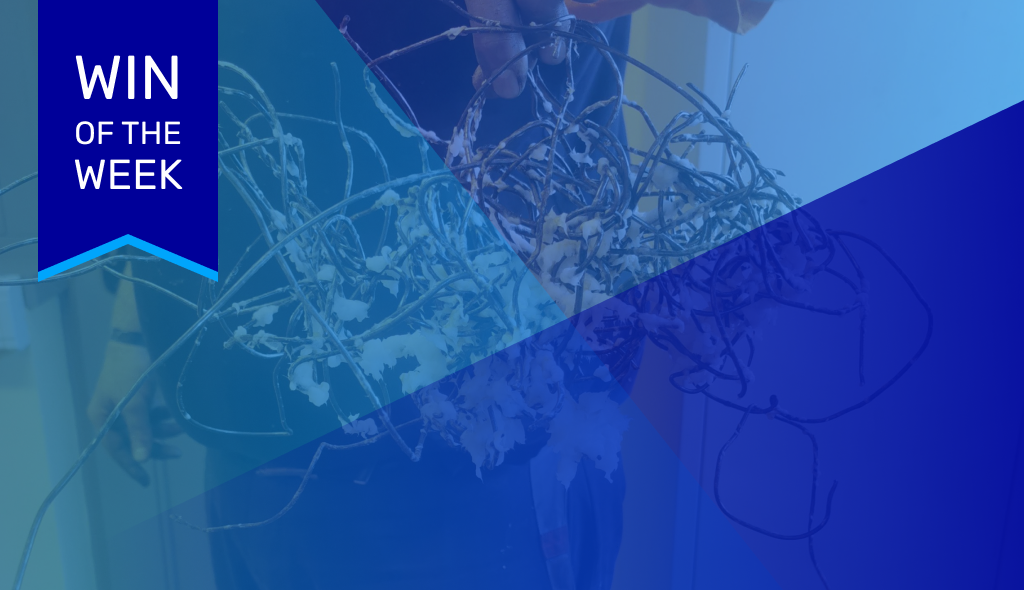
Augury delivered a big machine win for a global leader in paper tissue products by promptly identifying an operational issue — debris in a pump at one of their tissue manufacturing plants. With early detection and intervention, technicians were able to not only prevent damage to the pump, they also averted the tremendous problems the debris would’ve caused had it been allowed to travel into downline equipment.
Industry – Paper Goods //
Machine – Driven Pump //
Fault Type – Operation Issue //
Image 1:
Machine Health status, alerts, and communications between Augury vibration analysts and the onsite team are tracked and logged in the Augury platform as issues are detected and addressed.
Image 2:
Augury’s algorithms analyze over 840 unique feature sets. Below, turning speed amplitudes for the pump spiked, prompting the vibration analyst to trigger a machine health status alert. Amplitudes then decreased after the repair
On August 25th, Augury’s vibration analyst downgraded the machine health status of a critical driven pump to Alarm when the amplitude in the turning speed of the pump spiked to 0.6 inches per second.
Having full trust in the Augury solution and the vibration analyst’s recommendations, technicians responded rapidly, within two days of receiving the notification. When they opened the machine for inspection, they found debris in the pump — a tangled mess of metallic wires.
Image 3:
Metallic wires found in the driven pump (coated with bits of wet paper which had been suspended in the liquid inside the machinery).
The wiring was removed, having a positive effect on the machine’s behavior. Subsequent amplitude readings were less than 0.05 inches per second, resulting in a 91% decrease in turning speed amplitudes. The machine status was soon upgraded to Acceptable.
This win was even more remarkable when considering that the pump only runs intermittently. Had the pump been monitored using traditional vibration analysis – with someone walking around with a data collector gathering a four second snapshot just once a month – the problem would likely not have been detected until it was too late. The wires would’ve caused unchecked damage to the pump over a period of days or even weeks, and possibly wreaked havoc in downstream systems.
Want to learn more? Just reach out and contact us!