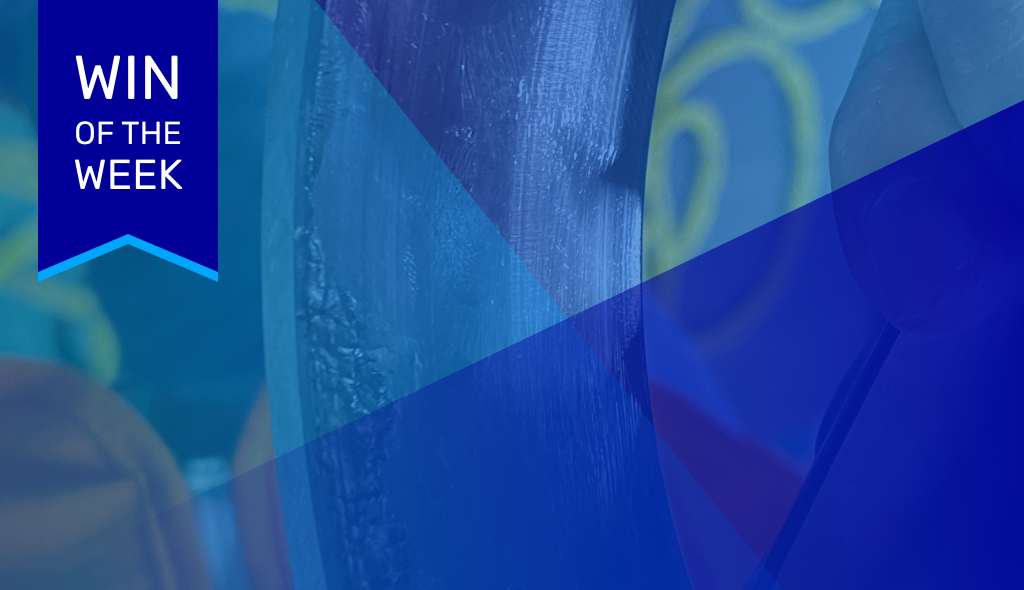
This Win of the Week, featuring a well-known CPG manufacturer, demonstrates the power of Augury’s continuous AI monitoring coupled with the support of expert vibration analysts. Augury’s vibration analyst collaborated with the onsite team at their home care products plant in Mexico, helping them work through a series of issues on a main fan that is critical to their production process. These issues would have resulted in catastrophic failure of the fan had they not been detected and addressed earlier.
Industry – CPG //
Machine – Fan //
Fault Type – Bearing Wear //
Image 1:
Machine Health status and alerts are tracked, logged, and visible to the Augury vibration analyst and on-site teams in the Augury platform as issues are detected and addressed.
Initial baseline measurements soon after the machine was connected to the Augury platform revealed high fan bearing vibration levels and motor misalignment. After the vibration analyst set the machine status to Alarm and alerted the onsite team, they changed the fan shaft and replaced the motor bearings.
The repairs reduced the vibration levels for the motor, but the fan bearings were still “noisy” for both the drive end bearing and non-drive end bearing. The vibration analyst set the machine health status to Monitor to watch for future trending.
Image 2:
Augury’s algorithms analyze over 840 unique feature sets. Shown below are the trends for fan bearing wearing as the machine’s health status changes from Monitor, to Alarm, to Danger (when a cliff was triggered), to Acceptable (after successful repair)
A few months later, Augury’s AI detected an outer race defect which was growing rapidly at the fan drive end bearing, triggering a cliff. The bearing wear appeared to be in stage 3 of 4, so the vibration analyst downgraded the machine to Alarm and recommended replacing it at the next downtime opportunity. Hoping to delay the repair for just a bit, the onsite team greased the bearing and aligned the belt, which they noticed was rubbing against the machine guard. This reduced fan belt vibration levels, but the existing fan non-drive end bearing vibration persisted and continued worsening.
Soon after, the fan drive end bearing fault levels increased exponentially in a 24-hour period to stage 4. The vibration analyst downgraded the machine to Danger and notified the onsite team, recommending that the bearing be replaced immediately as failure was imminent. The onsite team stopped the fan that night — just in time to avoid catastrophic failure — and replaced the bearings. After replacing the sheave and bearings, vibration levels improved significantly, and the machine health status was updated to Acceptable.
Image 3:
The repair revealed significant wear in the inner side grooves of the fan side pulley due to the excessive movement.
This win is a testament not only to Augury’s ability to detect machine health anomalies early and accurately, but also to the important partnership an onsite team can and should leverage with the Augury vibration analyst team. They worked together to provide feedback, confirm a diagnosis, verify the effectiveness of repairs … and save a critical machine while avoiding unplanned downtime.
Want to learn more? Just reach out and contact us!