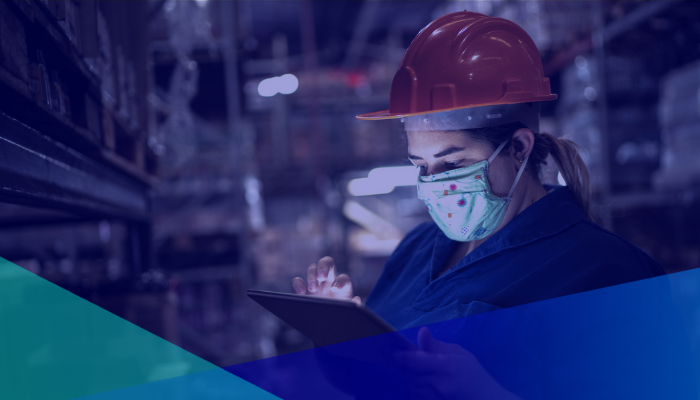
Before COVID-19, the concept of remote work hadn’t caught on in manufacturing as it had in other industries, and for fairly obvious reasons: people need to be on-site to accomplish most tasks. But manufacturing is experiencing a virtual shift that can positively impact the way manufacturers work even after the pandemic recedes.
The term “virtual shift” refers to work that was formerly confined to the factory floor but can now take place in virtual environments. The maintenance department, in particular, has embraced the virtual shift as a way to both extend and improve their efforts to keep machines in optimal shape.
At first, it sounds counter-intuitive that maintenance staff would perform better by interacting with machines virtually rather than physically. But machine health monitoring systems make the virtual approach efficient by supplying technicians with a steady stream of data including key machine health metrics like temperature and vibration. With prescriptive alerts that analyze minute aspects of machine health, technicians know when problems will happen and can intervene early — either personally or by directing someone else on-site.
Here’s an example: A piece of equipment produced in Italy breaks down inside an American factory. The factory could pay to import a master technician to diagnose the problem directly, but that comes at a huge cost and means the fix is days or weeks away. With a machine health monitoring system in place, however, Italian experts could review the data, diagnose the problem, and then walk on-site technicians through the fix — all without leaving their desks.
Thanks to the virtual shift, fixing the problem takes less time, costs less money, and returns production to normal faster. It’s an unorthodox approach to servicing equipment with positive implications for the entire industry.
The Future of Advanced Manufacturing
The virtual shift best describes the transition from the basic manufacturing of the past to the advanced manufacturing of the future. That’s because it allows factories to optimize all their critical resources, mechanical and human, through remote collaboration.
On the human front, advanced manufacturing technologies like a machine health monitoring system can allow one dedicated reliability engineer to serve multiple facilities. Instead of having a specialist stationed in each factory, a single person can monitor data coming from several sites, thereby cutting labor costs and making up for talent shortages. And by having someone monitor that data consistently, remote technicians can catch small problems before they lead to breakdowns — optimizing the effectiveness of equipment and minimizing the time and money spent on maintenance.
Moving forward, factories will be less driven by the resources they have on-site. Instead, they will rely on a network of experts and partners who have visibility into individual factories and specific pieces of equipment. Put simply, every factory will do more with less thanks to the power of remote collaboration to seamlessly deliver valuable resources wherever the demand exists.
Machine Health Data: The Missing Link
Manufacturers need the will to experiment with the virtual shift, but even more importantly, they need the underlying technology to make it possible. Without this technology, off-site locations are simply out of the loop. Remote collaboration can’t work unless those involved, especially those off-site, have access to real-time machine health data as broadly and deeply as possible.
Currently, most manufactures have symptom-level data that reveals the presence of a problem but does nothing to indicate the root cause. This data is basically useless to an off-site technician because to make any useful determinations, the technician would still need to travel to the factory to engage directly with the machine. Remote collaboration becomes impossible.
The missing link is the right machine health monitoring system to first track machine health data on a granular level and analyze it for early warnings of potential problems, then distribute that data to off-site observers. These two capabilities can bring the machine (and the underlying malfunction) into stark relief.
With all the right pieces in place, advanced manufacturing arrives sooner than many thought possible. Early adopters will be both the first to reap the rewards and the benefit the most in the long term. All it takes is an investment in the right advanced manufacturing technologies and a serious commitment to trying something new.
Want to learn more? Just reach out and contact us!