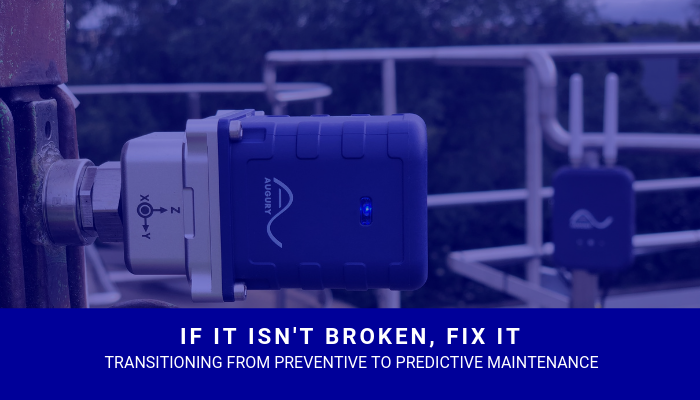
Preventive maintenance is similar to how most people service their automobiles. They don’t wait until the engine blows up to change the oil. Instead, they do oil changes, tire rotations, and other routine maintenance tasks on a prescribed schedule to prevent breakdowns in advance. They invest in the asset in order to maintain the level of performance that currently exists, for as long as possible.
In a factory, a similar preventive maintenance philosophy means skilled techs walk prescribed routes through the facility to manually check machine health and take recordings. In some instances, there is a reliability engineer in-house who can analyze the recordings promptly and recommend repairs as necessary. If not, the recordings are sent off-site, and there can be a long and sometimes costly delay in analyzing the recordings.
But, what if the machines could directly notify their maintenance professionals when they needed to be repaired?
To use the automobile analogy, predictive maintenance is when your car is able to tell you exactly when to change the oil. In a preventive maintenance scenario the owner would assume that the oil would degrade and lose function on some preset schedule, or at some predetermined mileage, so they would schedule to have the oil changed before then.
But with a predictive maintenance solution from the Industrial Internet of Things, the automobile would instead have sensors installed in the engine and the vehicle’s owner would possess a more complete understanding of the engine and its components, including the oil. Based on the real-time data provided by the sensors, the vehicle’s owner would only change the oil in the car precisely when needed.
In factories, this kind of predictive maintenance becomes possible when smart, cloud-enabled sensors are installed on machines. With modern continuous diagnostics solutions, sensors listen to machines, analyze the data, and notify maintenance professionals when repairs are needed before the machine fails.
Making the Transition from Preventive to Predictive
It’s always easier to implement new technologies when you aren’t currently fighting fires or pushing to meet production standards- so it’s important to select a technology that works for your assets, a partner that understands your business, and an internal team that can help you achieve your reliability goals.
Companies should start by considering the assets they have and how to protect them best. Vibration analysis is the most common method for protecting rotating equipment. But in a switchyard, for example, starting with infrared thermography or acoustic ultrasound emission makes more sense.
From there, companies should look for a technology partner that understands their needs and can guide them through the entire transition. If planned correctly with an experienced partner, implementing PdM can be a near instant relief. By the time your scheduled installation arrives, maintenance engineers should have a decent handle on preventive maintenance standards and be prepared, and excited, for the initial rollout of your new PdM solution.
Focus On More Impactful Work
Successful programs tend to select and create their own internal reliability teams. This group of engineers is embedded into the maintenance or engineering department of the operation during the initial rollout. After full implementation of a true predictive maintenance solution, maintenance technicians can spend their time focusing on the tasks that have the biggest impact. They’ll finally be able to utilize the advantages of continuous monitoring and advanced data analysis to identify potential fires before they happen – and take action to prevent them.
Moving from preventive to predictive maintenance is complex and takes time. I recommend considering your assets, choosing a partner that is committed to customer development, and investing in on-site reliability engineers who will help maximize your ROI on the technology investment.
See how Augury can help you make the transition to PdM! Learn more.