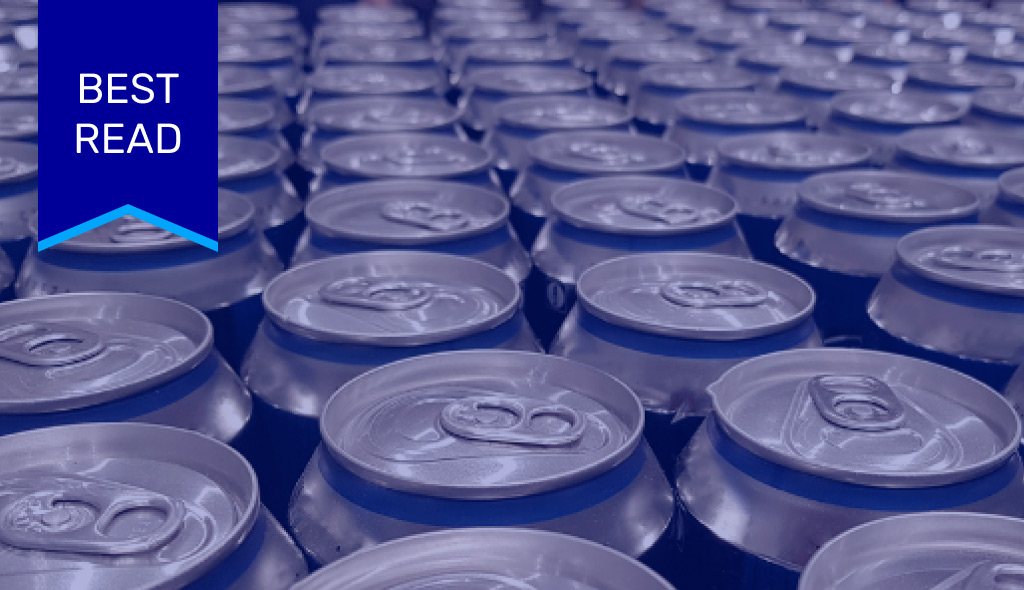
The line was running at full capacity, pushing out cases of beer in anticipation of game day. The Superbowl was right around the corner and product demand was rising as quickly as the excitement of the thirsty Rams and Patriots fans.
This article was originally published on June 25, 2019.
If It Works, Why Fix It?
As he logged in to the platform to check a machine health alert he received that morning, the Plant Maintenance Manager was a bit skeptical. He’d initially doubted the investment in the continuous monitoring machine health program that had been paid for by corporate.
Original Equipment Manufacturer (OEM) maintenance recommendations had worked fairly well in keeping their assets more or less functional through preventive maintenance tactics. And most problems were simply worn bearings from lack of lubrication or misalignment here and there.
He didn’t really see the value in dealing with anything more complicated. As long as the assets in his care didn’t critically fail unexpectedly and interrupt production, everything would be fine.
Worst. Timing. Ever.
But today was different. The alert he received pointed to a bigger mechanical issue than normal. This signaled a possible emergency within the plant’s filler and seamer equipment. This malfunction could bring down the whole line for hours or longer.
This couldn’t happen at a worse time. Right before the Superbowl—management would get involved and he didn’t need the scrutiny.
Empowered to Act Fast
Using his remote monitoring platform, the Maintenance Manager confirmed that the sensors were correct. They had to act fast. He alerted the repair team to the problems with the filler/seamer and they quickly diverted production to another functioning line.
By shifting as soon as the problem was detected, catastrophic failure was avoided and the equipment repairs were made without expensive, unplanned downtime. Soon, the production line was back at full capacity, overtime costs were mitigated, and the beer was saved.
The plant avoided a catastrophe that would have lost 960,000 cans of beer by fixing the filler and seamer malfunction before it halted production. The unscheduled downtime for their 24/7 operation could have lead to reputational risk with long-time customers—in addition to profit and production loss.
“It certainly would have taken the whole machine out, which would have halted the line for eight hours or more,” he later recalled.
Canning Concerns
Beverage manufacturers choose aluminum cans because they’re airtight and light-proof. This ensures product quality while still being lightweight, stackable and recyclable. But packaging success still depends on plant equipment working flawlessly.
The seamer is one of the most critical parts of a can production line because the double-seaming process ensures the package is sealed completely. And this has to happen as soon as the can is filled. When misaligned rolls or eroded chucks in the seamer equipment don’t fold the can body flange and top curl together accurately, the result is incomplete seals that lead to leaking or spoiled product.
Variations in temperature, machinery looseness, and wear can all cause problems with seamers on a canning line. Toolings can be loose or the chuck and roll can be set up too close or too far apart. This results in split seams, low or high free space, or high seam gaps, among other problems. Issues may also rest with the aluminum can bodies themselves—because the material is easily bent and microscopic differences can result in inaccurate seaming.
A Million Beers at Stake
Sometimes, a problem in the seaming is detected at Quality Control. This gives technicians a heads-up that values are out of specification, and that equipment needs to be adjusted. But manual tests take time and expertise. In addition, minute issues that can’t be detected by the human eye can be easily overlooked.
The margin of error was huge that day. Nearly a million cans of beer were at stake and more if there were issues responding to the repair process after a breakdown. Besides the lost product and repair costs, eight hours of unplanned downtime would lead to unanticipated labor and shipping costs as delivery schedules could be thrown off. And if some of the product made with the malfunctioning seamer was accidentally shipped, it might spoil. And this leads to expensive, and reputation-damaging, product recalls, or even legal action.
Trusting Technology
For beverage manufacturers working on tight timelines while prioritizing product quality, it’s clear that machine health plays a crucial role in their success. Smart and advanced sensors can monitor and protect the canning process at every step.
Monitoring the main drives on core machines, pumps, packers, fillers, seamers, conveyors, and labelers can ensure that even the earliest developing machine faults are detected the moment they arise—and disasters can be averted.
Big Savings, Speedy ROI
After this save, the Maintenance Manager was sold on this continuous monitoring machine health program. Not only had he kept the line running, but he’d saved an estimated $300,000 in unplanned downtime expenses. That, plus the saved product, added up to an ROI that was 10 times greater than the initial rollout cost. Corporate was pleased to hear about the great success.
As a result, the sensors were later extended to the plant’s other can and glass lines to provide further machine health insights that had the potential to save even more time, money…and beer.
Click here to learn more about continuous machine health monitoring.