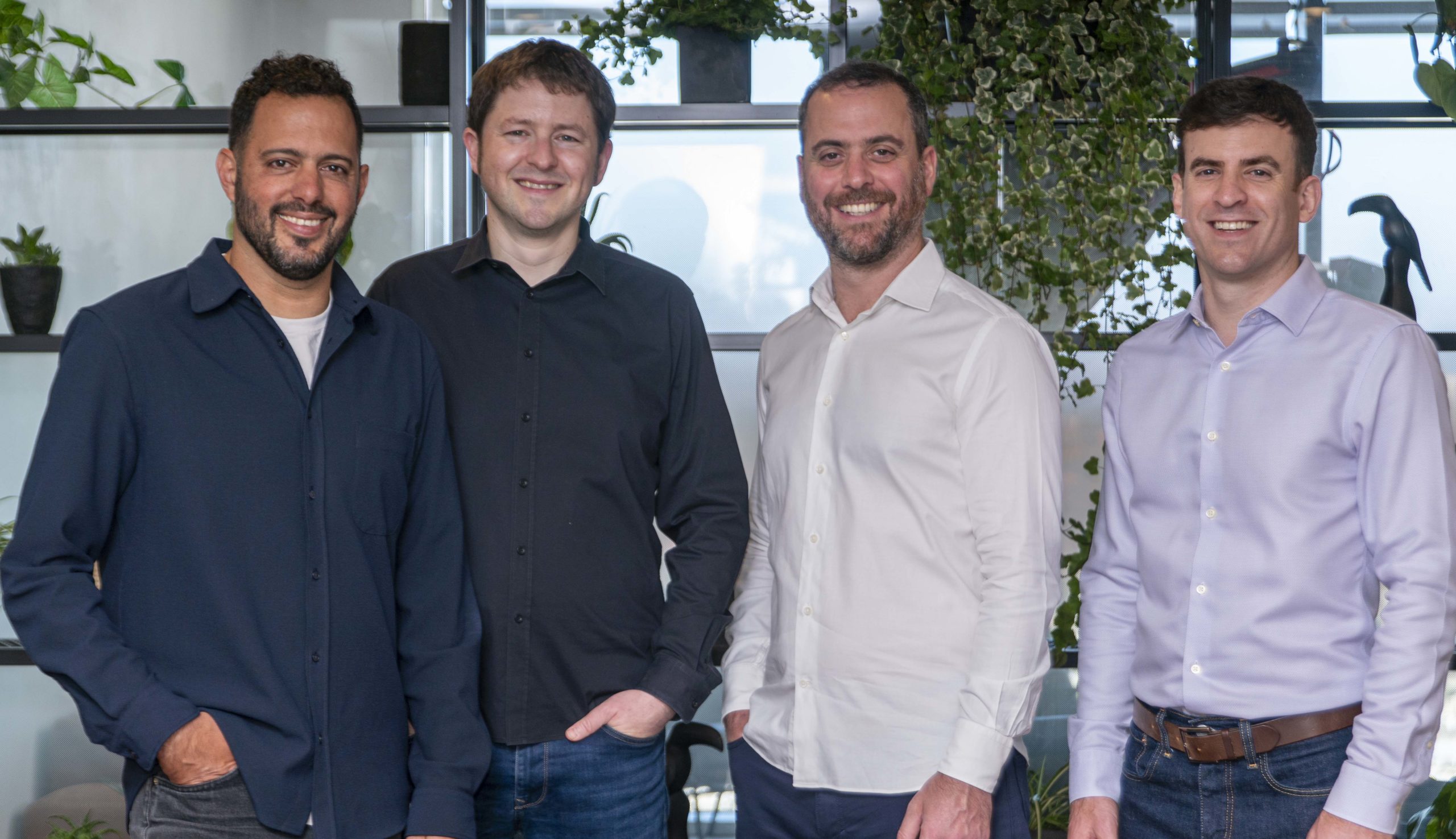
With Seebo’s process health solutions on board, Augury is showing how the world can solve some of its biggest challenges, such as unlocking the trillion-dollar gap opportunity that lies between current manufacturing effectiveness and the potential capacity of existing facilities – not to mention helping eliminate 10 billion tons of carbon-based emissions. Technology – specifically AI-driven technology – will lead the way, with Augury at the forefront of this movement.
Manufacturing leaders are painfully aware of their lost profits. It only makes sense to them when a paper shows that they could save 12-15% on energy consumption if their machines were all running optimally. They nod knowingly when a report states that $3.3 billion in waste is created through unplanned downtime alone due to defects in product. Manufacturers also know they will need more capacity in the future, but their only current option is to build new expensive and often-unwelcome factories, and try to find the skilled workers to run them.
Then there’s the trillion-dollar challenge itself… It’s estimated that “unplanned downtime is costing the process industries at about $1 trillion per year in lost production and revenues,” according to a report from ARC Strategies. “While many cite operator error as the primary reason, the process design or equipment controlling the process could, in fact, be bigger factors.”
This is exactly what Augury can now bring to the table: the right information at the right time – from across the production process – so operators can make the right decisions to avoid downtime.
The solution lies in part with a more activated workforce, according to the 2017 report. “To avoid an incident, operators must receive better information and training to make the right decisions. Operators must also be empowered to make these types of decisions based on their training and the available information.”
This advice may sound familiar since it’s the premise behind methodologies such as IWS and TPS which envision cross-functional teams collaborating to drive improvements in production, quality and efficiency. Unfortunately, the correlated data and insights those teams need to be successful has been impossible to come by and thereby limiting their effectiveness.
This is exactly what Augury can now bring to the table: the right information at the right time – from across the production process – so operators can make the right decisions to avoid downtime.
A Match Made In Production Optimization Heaven
As one of the first unicorns in industrial AI, Augury is already a proven entity when it comes to reducing and eliminating unplanned downtime. But now with Seebo’s best-in-class process health technologies in the mix, Augury can leverage AI-driven insights across machines, processes and operations in ways that can unlock fundamental transformation across the industry.
“When I look at what Augury does and what Seebo does, I see two proven technologies that have already created significant value to their clients,” says Lior Akavia, Co-Founder and CEO of Seebo. “And when these two technologies come together, I see a very tangible value that we can create to an enormous number of manufacturers around the world. For many manufacturers, this is an opportunity to make a leap forward and leverage AI in order to bring their production potential to its maximum.”
“When the process health solution can leverage the machine health data, we will be able to get better insights,” says Lior. “For example, we will be able to explain why waste happens in relation to mechanical faults in the machines – and that’s something no one is able to do today.”
It also works the other way around. “The machine health solution will now be able to not only alert when a machine is going to fail, but also, for example, to advise the manufacturing team on what settings will slow down the mechanical degradation,” says Lior.
“We can now provide a holistic solution to our clients, but also better value in both process health and machine health. And that’s something which is critical to enable our clients to reach their full production potential.”
Bringing Shadow Factories To Light
“Over the past decades advances in data analytics and process methodologies helped companies transform how they engage with customers and develop products,” says Saar Yoskovitz, CEO of Augury. “But the people in charge of the most complex operations have largely been left flying blind, lacking accurate insight into the combinations of factors that they need to optimize everything from equipment reliability and performance to quality, yield and efficiency.”
In fact, with the trillion-dollar gap between current manufacturing effectiveness and the potential capacity of existing facilities, there are whole factories lurking in the shadows just waiting to be unleashed. The solutions Augury and Seebo are bringing to the market, if adopted globally, would transform how manufacturing is being done – and how manufacturing impacts the world we live in.
“Closing that gap globally would not only drive massive increases in industrial capacity without the need to build new facilities but would eliminate the 10 billion tons of carbon that comes from production inefficiencies today,” notes Saar. “And it could all happen while making companies more profitable and workers safer and more autonomous.”
Stronger Together
To achieve full production health, specialized AI needs to work in tandem with an empowered workforce. Operations have become so complex it’s impossible to spot the combinations of factors that cause yield, quality or efficiency to fall short – or cause a production line to achieve a ‘golden run’ that would be ideal to duplicate every day.
“The human mind is simply not built to analyze hundreds or thousands of parameters that are constantly changing,” says Lior. “We need to continuously learn how the production line works, behaves and evolves. And this is where machines come into the picture.”
Armed with these AI-driven insights, humans can do what they are good at: springing into action to interpret and solve the problems in real-time – while adjusting their actions as new data-driven insights emerge.
And with humans and machines working in unison, the trillion-dollar gap will finally be bridged.
Watch: ‘Production Health Starts Here‘.
Want to learn more about the impact of our combined solutions: reach out.