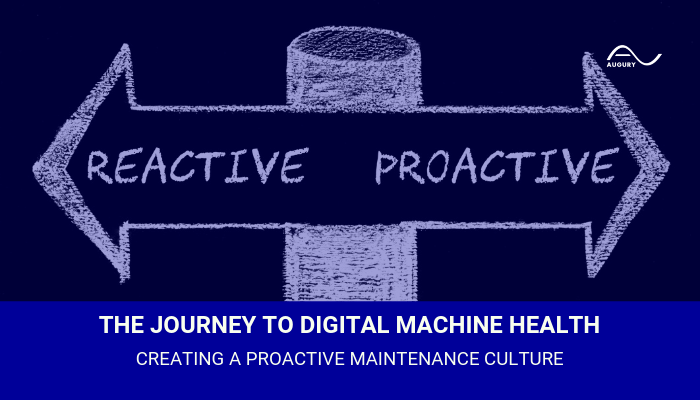
One of the key elements of Digital Machine Health is a proactive maintenance culture. Here are six simple steps that you and your organization can take to create such a culture.
Almost a year ago, an industrial manufacturer decided to implement continuous monitoring with Augury. Their machine maintenance team was accustomed to being reactionary. Not only in the way they dealt with scheduling and executing repair tasks, but also in their processes—such as using quarterly vibration analysis services that only provided “moment-in-time” snapshots of the operating condition of their assets.
Shortly after implementing their new Digital Machine Health solution, they received their first health report. It was eye-opening. A significant portion of their process and utility equipment were exhibiting extreme levels of vibration, indicating that major mechanical malfunctions were already present or imminent. At Augury, we anticipated pushback from the site level team, as the report put a spotlight on the operating condition of some of their most critical assets—but that wasn’t the case.
The machine maintenance team embraced the transparency and quickly worked with customer success to develop a phased action plan. They decided to focus on the machines with the most severe faults first and work their way down. Within three months the facility had all of its critical assets operating safely and efficiently. Seeing these results made the team confident that the insights provided by continuous monitoring would enable them to get ahead of mechanical problems, prevent failures and reduce unplanned downtime with a proactive maintenance culture.
Prioritizing machine health and enabling plant personnel with useful technologies and insights leads to a more productive and proactive maintenance culture. Keep in mind though, technology alone cannot help you achieve machine health—site-level buy-in and adoption are essential for a true cultural change.
Here are some simple steps that you or your organization can take to transform into a more proactive maintenance culture.
1) Be The Change
For organizational culture to actually change, it needs to be led from the top, with managers and executives employing a set of tactics to start driving the transformation. But even with leadership from the corporate level, facility and operational level buy-in is crucial. Key stakeholders from the teams who will be using the new tools and held accountable for the new programs need to be included and consulted in the decision-making process to bring in new technology. The users must understand and see the potential value of implementing the new technology at scale. It needs to be approached as an initiative to transform the organization as a whole and not a short-lived “science project.”
2) Enlist Influencers
In every facility, there are champions and up and comers who are eager to do their best, but rarely have time to work on new projects. That’s because they’re the people who step up when problems arise. The individuals and employees with extreme knowledge and the respect of their coworkers are the best champions of new products and solutions. They will be the best influencers for the new initiative and need to be brought on-board early. It’s also helpful if they are given a platform to share their successes.
3) Create A Vision
Culture change needs a clear vision, and goals. Managers need to help employees imagine a better and less stressful maintenance culture. Sure, at first it’s shocking to see that many assets may not be in the best condition, but what if you could get them all running in optimal shape and prevent them from downgrading again? Setting achievable goals including reducing downtime, increasing productivity, or optimizing PMs can help direct facilities and teams to commit to the program’s success.
4) Have A Plan. Stick To It
Everyone needs to be on-board with how to reach those goals. Corporate stakeholders need to align with plant leadership and the two must collaborate in developing the program in order for it to succeed. Once the plan is in place, it’s important to demonstrate ongoing commitment and communication between individual sites and corporate stakeholders. Finally, regular employee training helps increase buy-in across the operation and makes sure everyone knows what their part is in the new initiative.
5) Don’t Boil The Ocean
Cultural change isn’t about finding and implementing a simple solution. It’s a long-term shift that takes time, energy, and commitment. Being realistic about how much can be achieved, and by when, is essential. It’s the crawl, walk, run approach—while envisioning running from the beginning. Program leaders need to produce measurable results and allow for momentum to build as the wins start rolling in, faster and faster. You have to think about the big picture and understand that every small success means that you are heading in the right direction.
6) Kill Them With Success… And Data
For true culture change, implement software systems and data collection wisely.
Document how your sites are operating. Track successes and share your findings openly. Collect and compare data from facilities that are using the new technology and those that aren’t. Pay attention to the data that illustrates befores and afters to show the tangible changes that come from Digital Machine Health. The more your teams document, the more they will see the benefits of the program, which leads to more team buy-in and greater program success.
After implementing Digital Machine Health technology and ensuring you have representation at the corporate and site level, you can effectively pivot away from a reactive to a proactive maintenance culture. When supported and provided with the right tools for the job, the attitude and work habits of site-level personnel can transition away from simply fixing things when they’re broken, toward keeping machines running at their very best. In this way, Machine Health program leaders can quickly and effectively change organizational culture.
Are you curious about implementing Digital Machine Health? Click here to request a demo.