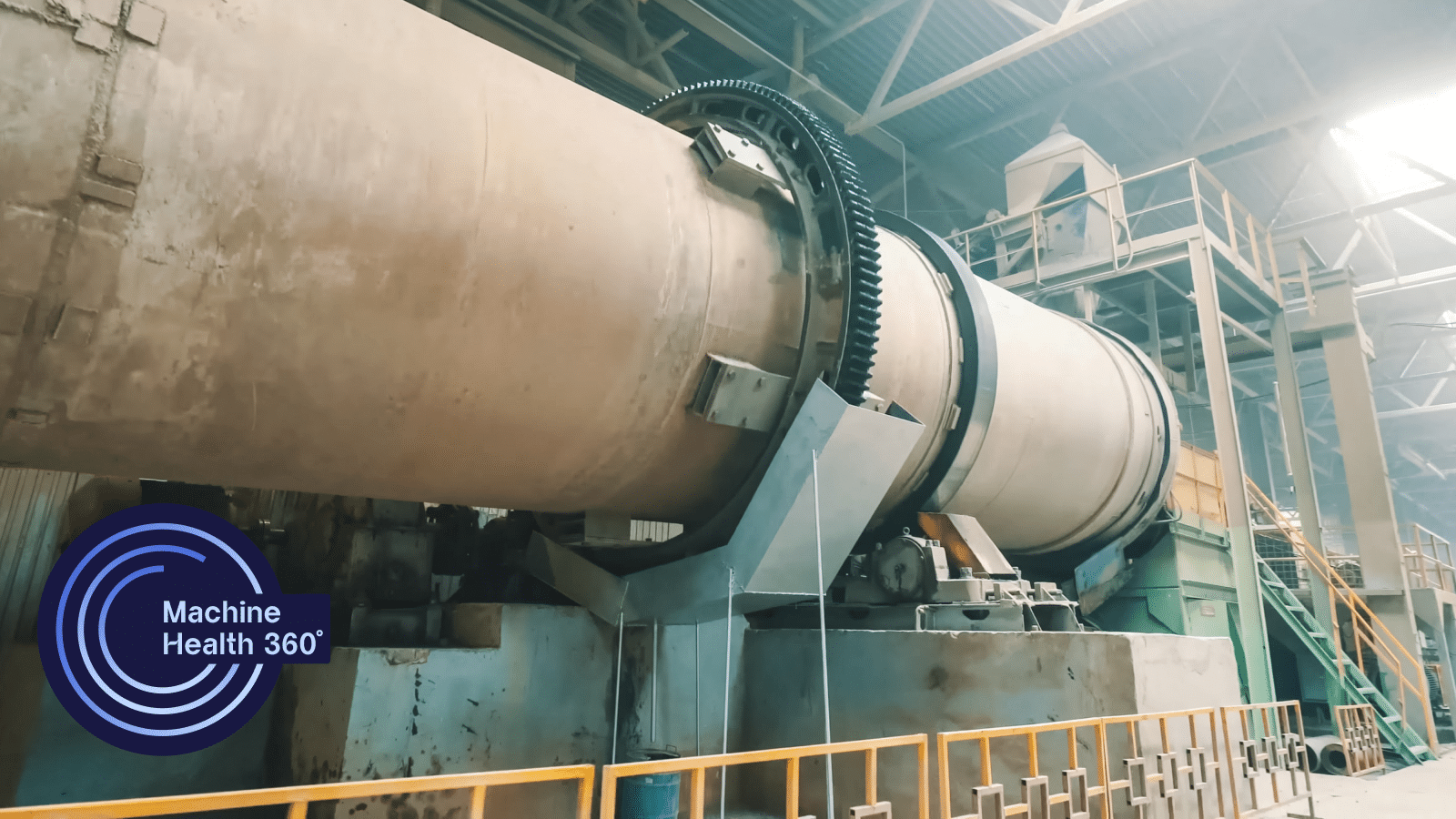
A few weeks ago, we hosted a webinar introducing Machine Health Ultra Low — Augury’s breakthrough solution for reliably monitoring slow-rotating (1-150 RPM) equipment. (If you missed it, you can still watch it here.) Since the session, we’ve received a lot of great questions. Below we answer some of the most common ones — and offer a deeper look into why the solution is changing the game for industries relying on slow-speed machinery.
What unique challenges do ultra-low RPM machines present?
Ultra-low RPM machines tend to have lower vibration energy overall due to their slower speeds. This means that faults tend to have very short spikes in the vibration waveform over long periods of time, which requires the collection of very long samples at a very high sampling frequency. This combination makes it exceptionally difficult to detect issues using traditional methods that capture short snapshots of data at lower sampling frequencies.
At Augury, we overcame these challenges by developing a solution that samples vibrations at extremely high rates (up to 100 kHz per sensor) and over a long period of time (up to five minutes long) to compensate for the extremely low energy vibrations of slow-moving assets. The result is reliable, high-accuracy machine health insights where other solutions fail.
Are you able to install endpoints on very hot surfaces?
For high-temperature applications, we install sensors using a drill-and-tap method. Our equipment can handle surface temperatures up to 250°F (about 121°C), ensuring reliable attachment even in demanding environments.
Will wireless ultrasound sensors be available soon?
While wireless ultrasound is technically possible, it comes with serious tradeoffs. One issue is battery life – the collection and transmission of large volumes of data will drain the batteries very rapidly. Wireless sensors can also miss critical fault detection beyond basic lubrication issues, sacrificing the quality and accuracy needed for true machine health monitoring. For this reason, our current wired approach is the gold standard for critical ultra-low-speed equipment.
Can Machine Health Ultra Low monitor feed conveyors that only run for a few seconds at a time?
It’s possible, but we would need more information about the application. For those interested, we’re happy to set up a meeting and explore the best solution for your operation.
Is it hard to develop a baseline if a rotary kiln runs multiple different products with varying loads?
Not at all. Our AI-driven algorithms are designed to adapt to various operational modes, even with changes in loading, mass distribution, and other dynamic conditions along the kiln’s length.
Where do you typically place the sensors on a rotary kiln?
For rotary kilns, we strategically place:
- Ultrasound sensors on the gear and pinions
- Halo R4000-series sensors on the motor (and sometimes on parts of the gear)
This ensures comprehensive coverage across the critical drivetrain components.
How low can you go with wireless vs. wired options?
Wireless (Halo R4000-series) sensors can monitor down to 150 RPM. Wired Ultra Low (Halo U2000) sensors can go all the way down to 1 RPM. If your equipment rotates extremely slowly, the wired Ultra Low solution is the ideal fit.
How does Machine Health Ultra Low compare to other solutions?
In short: they don’t compare. Competitors are not able to consistently achieve the 99%+ detection accuracy Augury delivers, especially for equipment rotating as slowly as 1 RPM. Ultra-slow machines present unique challenges that most systems simply aren’t built to handle — and it shows in their performance.
Is Machine Health Ultra Low already available?
Yes! Machine Health Ultra Low is fully available today. You can learn more here or reach out to our team to discuss deployment options for your facility.
Ready to take the next step?
If you have more questions or want a personalized assessment of how Machine Health Ultra Low can fit into your maintenance strategy, contact us — we’re happy to help!