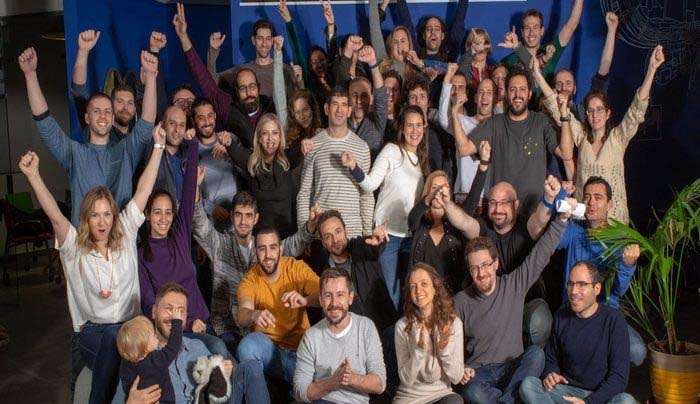
Here’s what Augury’s Reliability Success Team wants every customer to know when they start their Augury journey.
Our Reliability Success Managers are dedicated to making sure our customers get the most out of their Machine Health program. And in the process, they have observed what core habits help drive success. So, we reached out to them to ask what they consider the most important tips they have to share. Here’s what they came up with:
1. Identify – and train – the champions
Make sure you choose the right people who will be engaged with the Augury program – both at the corporate and facility levels. These are the individuals who will lead the rest of the team in adopting Augury and opening their eyes to all the value a well-run program can provide. By being the ones who will largely share the success stories, they’ll be able to increase the excitement and awareness of the program to the rest of the company.
2. Educate the entire team
People will be curious about what those little blue sensors are doing all over your machines. So you will need to educate the team – even those not directly engaging with the Augury program – on what we are out to do. Explain to them why we are collecting the data and how it will benefit the different stakeholders on the team. In this way you’ll have more buy-in and less animosity – and a much greater chance at success. Another bonus: people will be less likely to unplug a node to charge their cell phones (this has actually happened!). But you don’t need to overwhelm everyone. Only the primary users need the full in-depth training for the platform and hardware.
3. Make sure the maintenance team attends Augury Academy
Speaking of the primary users, everyone on the maintenance team should be encouraged to complete Augury Academy. They should be trained on not only how to navigate the Augury platform, but also how to maintain the hardware at the facility. It’s also better to have several people educated on how to use the Augury platform in case there’s an unexpected transition or personnel shake-up.
4. Realize Augury isn’t a program, it’s a culture
“Programs end. Augury is a culture. And this culture is saving downtime, money, and negative environmental impact at scale,” said the Corporate Operations & Safety Manager at NEFCO Biosolids. And this is very true. A successfully-run Augury program can have major impacts on the day-to-day workflow and operational procedures at a facility. For instance:
- Maintenance will likely shift from being unplanned to planned (meaning dealing with less, or zero, off-hour emergencies)
- Machines being monitored by Augury will likely have less unexpected downtime (again meaning dealing with less or no off-hour emergencies)
- Planned Maintenance (PMs) can be optimised for cost reductions thanks to the continuous flow of predictive insights on the machines being monitored
- Stock rooms can become more data-driven, and hence parts can be stored based upon their real-time necessity.
- Etcetera
And all of these have a large – and positive – impact on how each person goes about their workday…
5. Define your success metrics – and celebrate the wins
Everyone loves to celebrate wins. But wins need to be quantified and documented. So it’s essential for users to input downtime avoided and costs saved. The best performing companies will prioritize coming up with a quantification plan for each of the sites in the program, starting at the corporate level. We really want to be able to realistically quantify the impact of any “wins” so that the story can be shared with the team to drive further engagement.
6. Engage with the system!
Yes, you can sit back and wait for Augury to tell you what to do in terms of keeping a machine running. But you can also be more proactive in using Augury to your advantage. If you see something on the floor… When you have a question about a machine… If a machine is not performing well… If a machine looks weird, smells weird or sounds weird…
As our eyes and ears, you should log any such comment or observation at the machine page to trigger analysis from Augury’s team. While the Augury system is continuously monitoring the health of your machines, we can’t replace the importance of the boots-on-the-ground perspective. Operational insights and physical observations can really improve and focus Augury’s diagnostics on your unique machines at your particular facility.
7. Commitment to cadence calls
We’re here to help – anytime. But you don’t want to miss our regular “live” check-ins. We start off with bi-weekly calls until everyone feels comfortable enough to make it monthly. The length and frequency of these meetings will be determined by the number of machines monitored, and the ongoing number of machine faults worth discussing.
8. Don’t be shy
We got your back. Contact your Reliability Success Manager about anything and at anytime.
Also read ‘Innovator Insights: 5 Tips for New Augury Customers’ about how manufacturing innovation leaders at the Colgate-Palmolive Company were instrumental in the implementation of Augury’s program throughout the company’s global manufacturing operations.
Or just reach out directly to learn more about our AI-driven Machine Health Solutions.