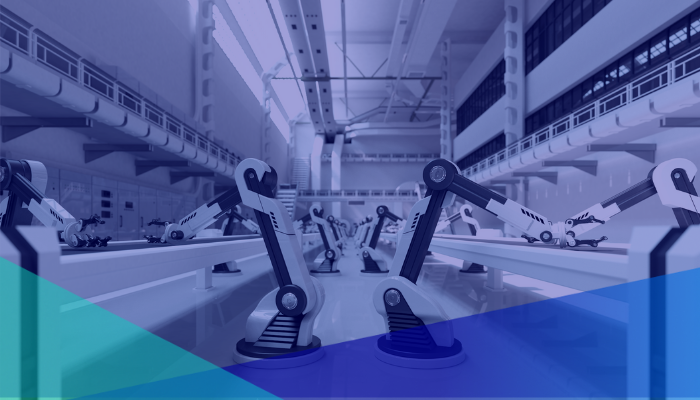
The pandemic has exposed the fragility of many supply chains as manufacturers struggle to get supplies and consumers confront empty shelves. In the wake of a disruption that happened faster, deeper, and with less warning than many thought possible, operational resilience has become a top priority for manufacturers.
Resilience means having a plan B in the face of anything, whether that’s a global pandemic, severe weather event, or sudden market disruption. A resilient factory has whatever physical resources it needs to maintain operations and whatever intellectual resources it needs to adapt to the unexpected.
For example, if one production facility had to scale back or suspend production in a resilient operation, decision makers would know where and how to ramp up production elsewhere to balance out the loss. On a smaller scale, if problems appeared on one production line, resilient factories would have an obvious and accessible plan in place with the capacity to take on the additional work. Regardless of the nature of the problem or the extent of the solution, resilient factories are equipped to proceed as close to 100% capacity as possible.
How Resilient Operations Drive Manufacturing Success
We may never see another pandemic in our lifetimes, but we will certainly see many of the weaknesses and failure points the pandemic has highlighted. Take maintenance, for example. Social distancing requirements made it more difficult to keep enough maintenance staff on hand to service machines, but maintenance based on reactive or preventive techniques was often inefficient before the pandemic — and it will be afterward, too. If anything, the events of 2020 revealed the consequences of letting this issue persist for so long.
That lesson seems to be resonating with plant managers and manufacturing executives who are increasingly adopting IoT technology and operational strategies. Tools like connected sensors installed on industrial equipment let managers monitor machine health metrics and, based on that data, initiate maintenance before malfunctions can cause production delays. Advanced analytics applied to machine health data can even diagnose the issues and prescribe the solution in the form of step-by-step instructions for technicians to follow.
Predictive maintenance and machine health monitoring solutions boost resiliency in many ways, particularly by automating alerts for maintenance activities. These actionable alerts help technicians complete a higher volume of work with fewer technicians on-site. Connected sensors used in conjunction with remote collaboration technologies can also allow specialists located off-site to monitor machines and guide the limited staff on-site through any work required. A resilient factory has robust maintenance capabilities even with a skeleton crew on-site.
The benefits of resilience are both operational and economic. For instance, if a factory can use machine health monitoring to essentially failure-proof its production lines, it becomes more attractive to customers and more competitive in the market. In that way, IoT in manufacturing helps producers make their maintenance strategy and their business model more resilient.
Moving Toward the Factory of the Future
Resilience isn’t a novel concept in manufacturing. The factories of the past tried to make themselves immune to the unexpected using a strategy of redundancy, where they would have whatever backup machine or spare part they might need inside the facility at all times. Necessary as this approach may have been, it was a drain on resources that rarely worked as intended. Case in point: Social distancing requirements made maintenance difficult, even with an army of technicians available.
The factory of the future achieves resilience using an opposite approach based on assets being smart, lean, and agile. Instead of preparing in advance for every kind of contingency, manufacturers can put tools like IoT technology in place that give them foresight and flexibility. Tomorrow’s factories will put themselves ahead of the wave of change by predicting things in advance and acting early. That proves to be the best form of resilience: where manufacturers evolve organically with the times rather than depending on the status quo to hold up under every sort of stress.
Machine health monitoring tools combined with a data-driven analytics platform make the resilient factory a reality exactly when unprecedented circumstances make it essential. Are you ready for the next disruption?
Want to learn more? Just reach out and contact us!