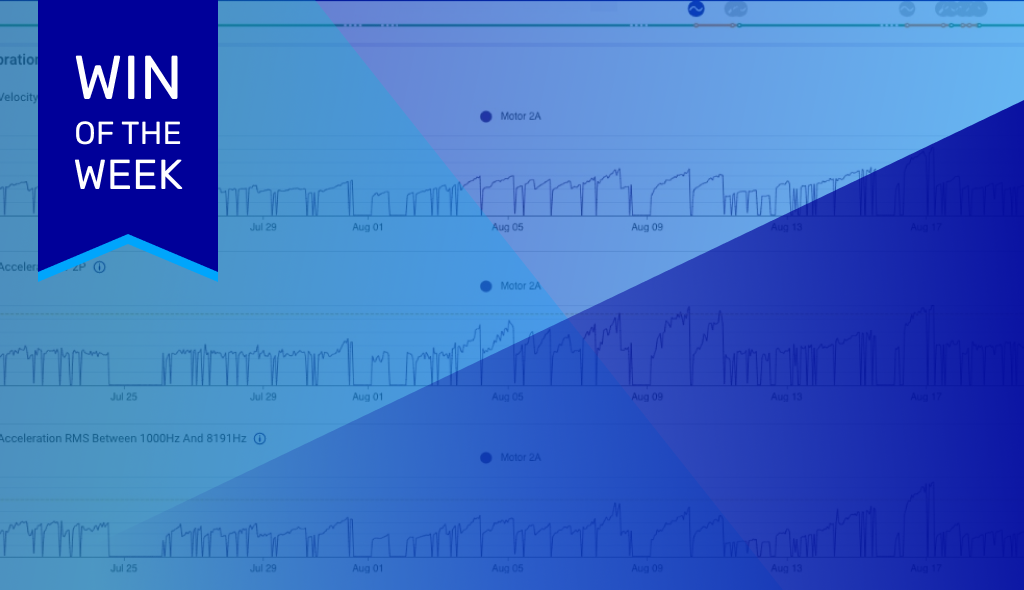
Seamers require an optimal balance of pressure in order to ensure product quality. Incorrect pressure can mean damage to materials and machine components. In this Win of the Week, see how Augury helped a large, multinational manufacturer prevent disruption to their diaper production line by identifying an operational issue with a seamer.
Industry – CPG //
Machine – Seamer Anvil //
Fault Type – Operational issue (Impacting, interference too tight) //
Image 1:
Machine Health status and alerts are tracked, logged, and visible to the Augury vibration analyst and on-site teams in the Augury platform as issues are detected and addressed.
Image 2:
Augury’s algorithms analyze over 840 unique feature sets. Changes and trends in Vibration Velocity RMS and Acceleration P2P, and Acceleration RMS Between 1000Hz And 8191Hz at time of the alerts are shown below.
It’s normal to see small fluctuations in vibration on a seamer when changing the size of diapers in production. Larger sizes, for example, mean more material and harder impact. However, when the Augury vibration analyst noticed a spike in the seamer’s vibration levels that crossed a threshold he had set, he alerted the onsite team and asked them to investigate. The symptoms of the vibration looked similar to past problems with interference fit, so it was recommended to start there.
Over the next few days, the onsite team first tried increasing the gap between the contact point of the seamer anvil and the seamer unit tooling, then resetting the interference between the unit and the tooling. The adjustments helped only temporarily. Further investigation found the seamer unit to anvil contact interference to be too heavy. Contamination build on the tooling over time was causing the vibrations spikes, which were traveling through other nearby components. Increasing the gap and cleaning the tooling lessened the interference and reduced vibration, and the machine was placed in Acceptable status.
Thanks to Augury’s 24/7 monitoring and constant trending, the vibration analyst was able to see slight vibrational changes and alert the customer before the machine was damaged and product quality was compromised. The issue would have otherwise gone unnoticed with a traditional maintenance route, leaving the machine running with elevated impacting vibration until perhaps a month later. Catching this operational issue early helped the customer prevent unplanned downtime, costly repairs, and product waste due to damaged materials.
Want to learn more? Just reach out and contact us!