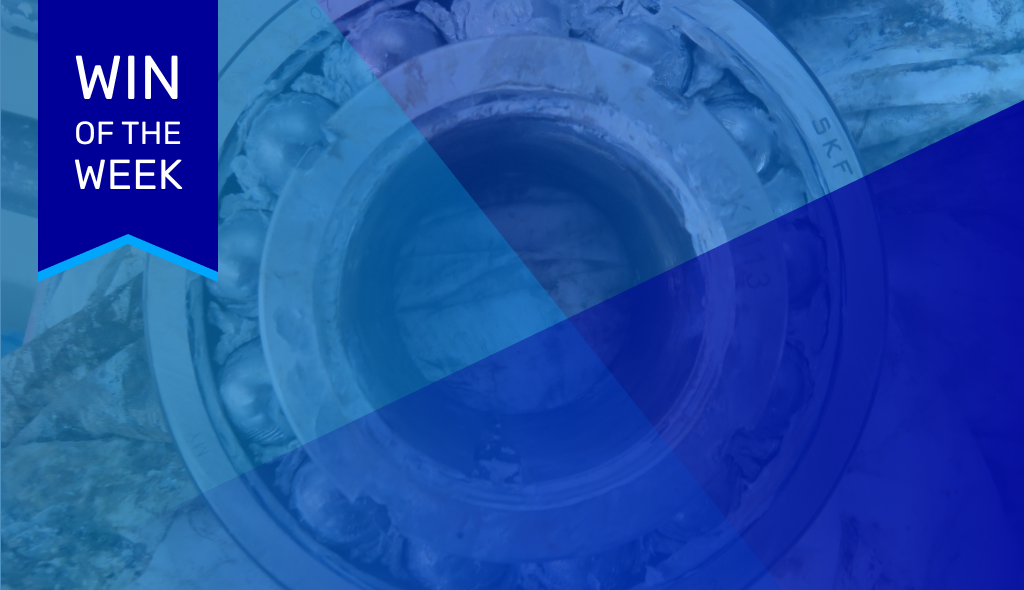
Machine Wins can happen right out of the gate as highlighted in this Win-of-the-Week which took place at a packaging plant for one of the top, most trusted pharmaceutical companies in the world. At this site — the customer’s first to come on board with Augury — bearing wear issues were identified straight out of baseline for one of their four process-critical fans.
Industry – Pharmaceuticals //
Machine – Driven Fan //
Fault Type – Bearing Wear //
Image 1:
Machine Health status, alerts, and communications between Augury vibration analysts and the onsite team are tracked and logged in the Augury platform as issues are detected and addressed.
Image 2:
Augury’s algorithms analyze over 840 unique feature sets. Below, the Detectors Confidence indicating the percentage confidence that there was a bearing wear issue began high and increased over time.
Within the first hour after the fan was connected to the Augury platform, the Detectors Confidence for bearing wear was already above 50% from the first reading. The vibration analyst placed the machine in Danger and recommended repairing the machine as soon as possible.
When first examining the machine, the customer’s third party contractor for fan maintenance didn’t discover any issues and simply lubricated the machine. However, when there was no improvement in the data and the Detectors Confidence continued to increase, the vibration analyst persisted, strongly recommending deeper investigation.
Image 3:
Scrapings on the ball bearing of the driven fan, a major fault indicating the machine was close to failing.
After the machine was finally opened up, significant damage was found — a major bearing fault. Even without being able to see the condition of the inner race and outer race, it was clear from the bearing wear that the machine could’ve failed unexpectedly at any time if not monitored.
Since replacing the bearings, the velocity and impacting indicators have been perfectly quiet and smooth. The customer was happy to see significant improvement in the values and was impressed by Augury’s expertise and ability to identify the damage. This early machine win helped the customer avoid impending machine failure and a potential line shut down. While the machine appeared fine, the truth was in the data.
Want to learn more? Just reach out and contact us!