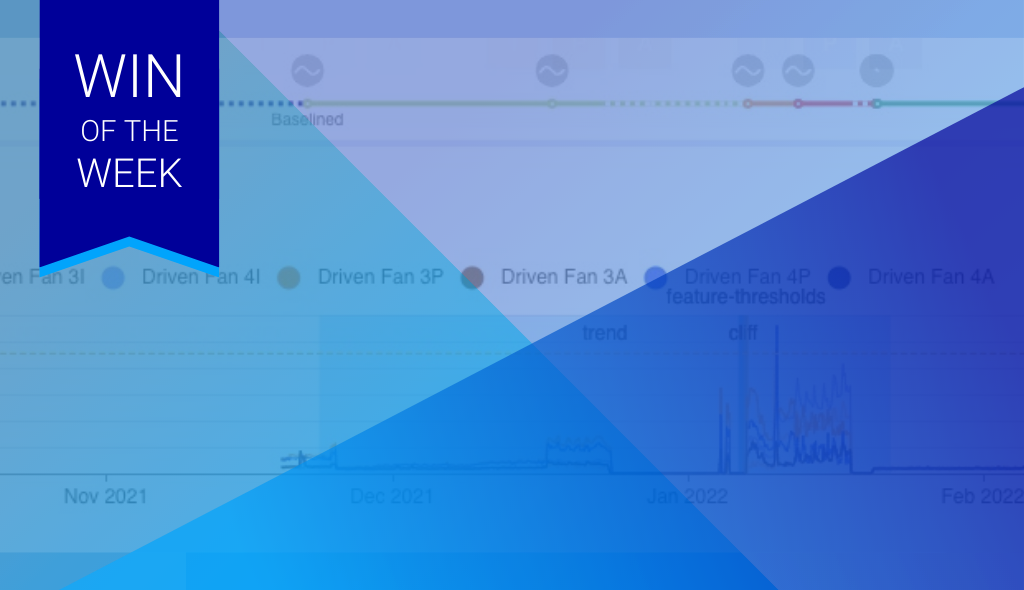
This Win of the Week demonstrates how Augury helped a global chemical manufacturer’s European plant detect and diagnose an issue with a critical flue gases fan, preventing its failure. What makes this an even bigger win is that the problem was identified shortly after installing Augury. The manufacturer had experienced the same issue on this machine two years earlier and knew what it had cost them—a catastrophic machine breakdown that involved three weeks of unplanned downtime, a loss of €210,000 in sales, and over €15,000 in maintenance costs.
Industry – Chemicals //
Machine – Flue gases scrubber fan – Fan (Driven Fan) //
Fault Type – Radial Unbalance //
Alerted to rapidly deteriorating machine health
During the baseline period of a flue gases scrubber fan, Augury’s Machine Health for Critical Assets (MH CR) identified a possible bearing fault, as well as misalignment between the motor and the machine. The machine’s health status was set to Monitor.
Soon after baseline, Augury’s vibration analyst saw the trend in the machine’s velocity RMS climb rapidly, with significant vibrations of 1.2 inches per second. He downgraded the health status to Alarm for radial unbalance, and noted that the recent increase could be due to a heavy spot, dirt build-up, or erosion of the fan blades. After a brief dip, the trend continued to increase over the next few days, with vibrations reaching almost 2 inches per second. The vibration analyst changed the health of the fan to Danger and recommended that the onsite team repair the machine as soon as possible, running it with caution until repaired.
Image 1:
Augury’s algorithms analyze over 840 unique feature sets. This image depicts the velocity RMS and shows a rapid increase in the driven fan velocity trends, indicating radial unbalance.
When the onsite team disassembled the turbine and inspected the fan, they discovered a heavy build-up of dirt. The team recognized that this was the same situation they had encountered two years prior, and that a catastrophic failure had been averted.
Three weeks of downtime avoided
A scheduled repair was carried out, including a high-pressure polymer cleaning, which alleviated the symptoms of radial unbalance. The fan was back to functioning normally, costing only €7,500 to repair compared to the €15,000 the manufacturer had spent to rebuild the fan after the previous failure. Additionally, production downtime was just three days compared to the three weeks required to replace the fan the last time, preventing over €200,000 in lost sales.
Because the issue developed so quickly, it would likely have been missed using traditional, once-a-month monitoring. But with Augury’s continuous monitoring, the fault was detected early, enabling the manufacturer to avoid damage to the fan bearings or worse, including breaking and having to rebuild the shaft (both costly and time-consuming), as well as preventing possible damage to property and injury to nearby personnel.
Image 2:
The flue gases scrubber fan with heavy build up before cleaning (left) compared to a clean fan (right).
Want to learn more? Just reach out and contact us!