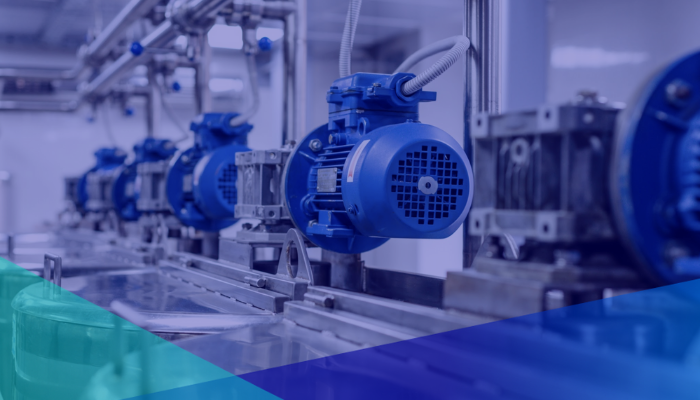
Overall equipment effectiveness, or OEE, is an important measure of your facility’s productivity. Measuring OEE allows you to rate the availability, quality, and performance of your equipment to determine how often it breaks down, whether it performs as designed, and how much scrap is produced.
Manufacturers allocate entire budgets and large-scale efforts to reach world-class OEE percentages, which industry standards place at around 85%. Improved OEE translates into higher-quality products, more efficient production, and more cost-effective maintenance for your machines.
You can improve the various components that influence OEE in many ways, but one key way is machine health monitoring. To understand the efficiency of your equipment and production lines, you need deep insights into the health and performance of machines. Here’s how machine health data can help you improve three important OEE factors:
1. Machine Downtime
Installing sensors and technology that continuously monitor and diagnose machine health while providing prescriptive insights for malfunctions eliminates unplanned downtime and improves the efficiency of planned downtime.
With predictive maintenance and machine health technology, you’ll know when your machines are likely to break down and exactly what needs to be repaired before malfunctions can halt your production. These actionable insights reduce unplanned machine downtime and help your team move into planned/scheduled maintenance with insights that will help them make repairs efficiently — while significantly increasing machine availability. This also helps reduce scrap by ensuring machines operate at optimal levels and helps maintenance teams eliminate issues before they start to negatively impact the quality of your products.
2. Facility Design
The advantages of machine health monitoring are mostly mechanical in nature and revolve around how machines perform. Yet several other factors outside of mechanical ones also affect OEE, including the overall design of your facility.
Having machine health data from each of your production lines can help you recognize consistent issues and identify which machine configurations perform the best. With those insights, you can reproduce your best-performing configurations and avoid known issues in every line, optimizing the overall design of your facility.
3. Operator Error
In addition to mechanics and facility design, operator error is another essential metric in operational effectiveness. Companies with low OEE can often attribute it to personnel who lack proper training and knowledge of operating procedures or who don’t follow the right methodologies. Machine health monitoring provides deep visibility into machine performance to help determine early on when and how operator behavior is negatively impacting OEE. It can also help drive a machine health training program to help your teams do what they do, better.
Each point of improvement in OEE can have a tremendous impact on productivity. Deep machine health insights and data that help you boost your OEE can translate into millions of dollars in savings and boosted revenue for your company. As you optimize the OEE for each facility, you can uncover additional capacity from existing assets, scaling your productivity significantly without having to invest in new facilities or machines.
Want to learn more? Contact Us for information or OEE or Overall Equipment Effectiveness.