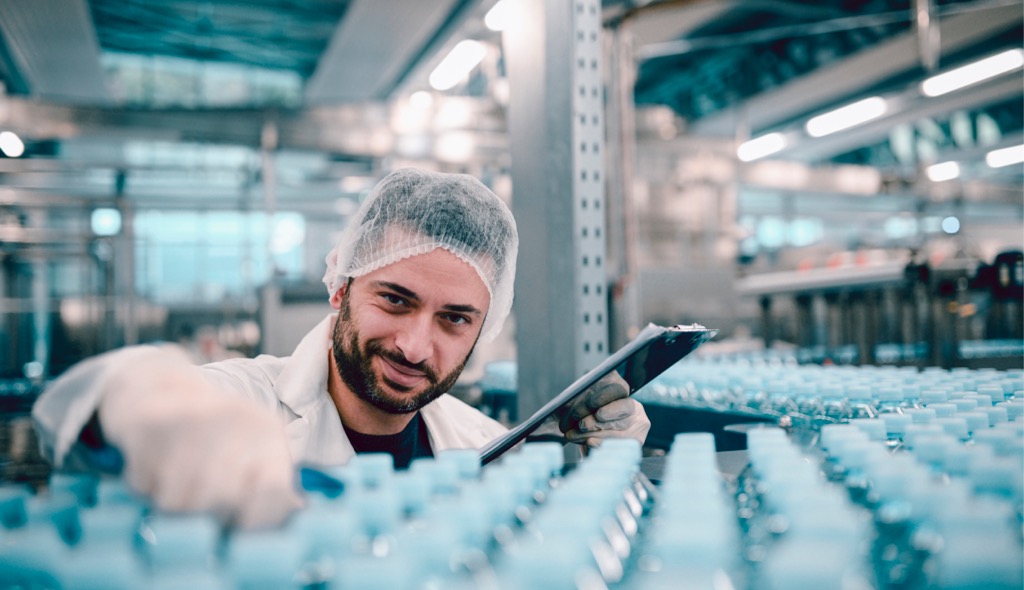
In a Packaging Digest article, Augury advisor Ed Ballina uses his experience as former VP of manufacturing and warehousing at PepsiCo to explain the benefits of Machine Health monitoring to improve equipment reliability and uptime when labelling plastic bottles.
Packaging Digest just published ‘How Machine Health Monitoring Can Improve Labeling Operations’ by industry legend Ed Ballina, who also serves as Augury’s Food & Beverage Board Advisor. The article describes the power of AI- and IoT-driven predictive maintenance – or ‘Machine Health’ – tools in improving process and eliminating waste and mechanical failure.
Machine Health monitoring can alert maintenance teams to issues and how to fix them – while avoiding downtime. While applicable to the full manufacturing spectrum, in this article Ed focuses on the specific benefits for labeling operations. After a quick lesson in how plastic bottles are labeled, he describes some real-use cases on how Machine Health monitoring can provide speedy ROI.
Read more about Machine Health Use Cases.
Use Case #1: Ensure Clean Cuts
When you are labeling 600-800 bottles a minute, visual inspection is simply not enough when it comes to making sure the cutter is sharp and the equipment aligned. The wasteful result: a surplus of ugly packaging that will be judged by the consumer, and/or unlabeled product that’s discarded as ‘mysterious’ once they reach the retail outlet.
“Predictive analytics can lead us to this real-time process monitoring of labeling performance,” observes Ed. “It can determine when the cutter blades dull to the point where they start cutting raggedly. At that point, we can exchange the blades for new ones — during regular downtime instead of an unplanned stop — making poor labeling due to bad cuts a thing of the past.”
Use Case #2: Beware of Label Variations
Another familiar problem for labeling operations: a seemingly identical new roll of material causes a litany of new problems.
“Analyzing Machine Health data from the ‘good’ running roll and comparing it to data from the ‘bad’ running roll is likely to provide clues,” says Ed. “Many times, insights gleaned from analyzing the data captured by the new technology tools confirm what frontline workers know anecdotally and have learned from experience.”
In short, the article is worth the read for anyone with a labeling line who is out to pump up their productivity.
Learn more about the value of using predictive analytical tools for labeling.