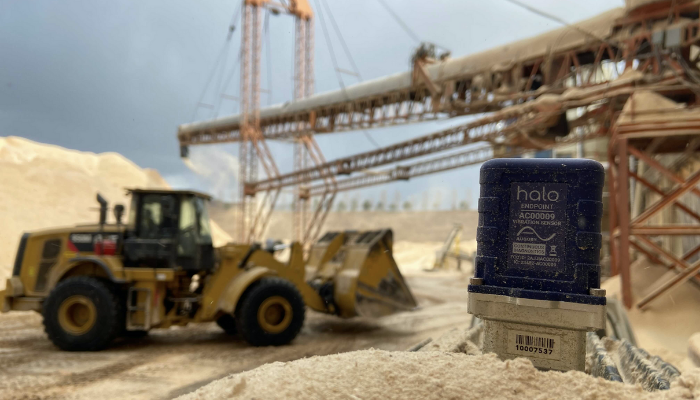
Roseburg’s Brian Richmond spent 20 years in the military, hopscotching across the world to Europe, Asia and other far flung places. So how did he end up back on a farm in Louisiana not far from where he grew up?
“I was born about 45 miles from where we live now,” Richmond says of his decision to take a position with Roseburg in Simsboro, Louisiana. “It’s been a very long journey to get back here, but it was kind of a weird journey I didn’t see coming. I’m glad to be back.”
As a regional reliability manager for Roseburg Forest Products, Richmond is responsible for process improvement, budgets, training, and much more.
Before arriving at Roseburg, Richmond spent two decades in the U.S. Navy, planning maintenance work on nuclear submarines and developing training programs for engineers. Richmond earned an MBA from Excelsior College, then relocated from the West Coast to Simsboro, Louisiana.
Here, in an interview, he discusses his career trajectory, how he unwinds during the pandemic in his “man cave” and the ways in which Augury and machine data have helped him transform Roseburg’s reliability programs.
You began your career in the Navy. What did you learn from your time there?
Brian in the Navy
I got to see all kinds of different cultures. We spent a lot of time over in Japan and Germany learning some of their techniques and processes. Underway on a submarine you don’t get a whole lot of spare parts so the reliability of your equipment is really one of the foremost things you’re trying to maintain.
My upward mobility in the Navy was very quick. By the time I had been in for five years, I had a department that I was responsible for and a lot of people who worked for me that were significantly older than I was.
It’s really hard to argue with experience. But what I learned quickly is that you have to have data. The person with the most accurate data and the most data can usually prevent an argument from even occurring. A lot of people with experience will be overbearing with you and say, “This is the way we’ve done it” and “This is how we’ve done it.” That’s really how I learned how important that data aspect is.
You’re from Louisiana. How did you end up back there working in a position with Roseburg?
After 20 years in the Navy, I really had no clue what I was going to do. The only job that really correlated to what I did there was power generation. Six months after I retired from the Navy, I was contacted by Roseburg to come work for them as a superintendent for a powerhouse in Oregon, then as a sawmill maintenance manager. I moved from Oregon to Louisiana and was promoted into a regional reliability manager role overseeing plants in Louisiana, Arkansas, Mississippi, South Carolina, Canada, Oregon, Montana and California.
I grew up in a farming community. We have land and animals. My kids are very wrapped up in animals, and my wife is applying to vet school this year because she’s very into taking care of animals. I moved from Oregon to Louisiana and most of the animals we have now, we had in Oregon. It is kind of weird to roll down the Las Vegas strip with two horse trailers, a llama, cattle and a bunch of horses. You get some weird looks.
Brian Cleaning a Stall
In this picture, I’m supposed to be cleaning that stall. I’m not doing very good because it’s of course one of those nights where I got home and about 10 minutes into the night, I get a phone call about a piece of equipment that’s broken. Really making that call, do I need to turn around and go back?
How does a typical day at work begin for you?
Every morning I’m usually up between 4:30 and 5:00. I would like to say that I go out and help with the animal chores, but I don’t. I usually start thinking and looking at my phone and figuring out what emails I need to answer. My wife basically makes my coffee and throws me out the door by about 5:15 or 5:30.
I have about a 35 to 45 minute commute to work. And in that drive, that’s when I do a lot of my thinking about what’s going to happen that day, what needs to happen that day. What problems didn’t I solve the day before?
Brian’s Desk
I log into my emails, and I go onto our dashboard to see what things I need to answer and what questions people have. I’m looking to see what my technicians are worried about. What did they fight last night? What help do they need?
My dashboard gives me the site overview for all our plants. This is critical because it allows me to figure out what plant I need to look at right now. If something came up in Augury or Tableau or on any one of our other systems that says, “Hey, we had a failure last night,” I’m going to go straight to it. I’ll make a phone call to the maintenance manager of the plant and say, “Hey, what happened with this? And what do you need?”
How did the COVID-19 pandemic impact you, your business and your employees?
One of the blessings we have as an organization is that during the COVID crisis, we didn’t shut any plants down. Our technicians and operations group all rely on us to really function day to day. We did tailor back some of our production times, but the wood products industry has done very well in general.
It was critical that we were able to keep the plants running, because most of our technicians are part of dual-income families. They needed to be able to rely on at least one of them, because one probably wasn’t going to last. We were able to fulfill that by proving our reliability by increasing our uptime, honestly, and by changing our profit margin to some extent.
Brian’s man cave and home schoolroom
A lot of times when I am stressed, I just want to work out. I’m an avid boxer, and I have a punching bag and boxing equipment. I also like billiards and darts. You look at this room and you see a man room but my two youngest kids are both homeschooled and it’s really turned into a great teaching base for them as well.
This whole (Covid-19) thing makes me able to help teach them, where in the past I was stuck in an office. It’s amazing how much physics you can teach a seven year old on a pool table. I’m grateful for the fact that we were not in a bad way and were forced to spend more time together at home because we couldn’t go places. That has really been a blessing to us.
How have data and technology improved the quality of life for your team?
One of the things we do is we patch things. We don’t really fix them. And we do that because we don’t see the break coming. We don’t see the failure coming and we have to get running right now. And if you get six or seven or eight of those patches on, when your failure occurs, it becomes catastrophic and now your downtime is significant. Technicians don’t want downtime. Downtime means they have to go there to work on it.
Roseburg wheelwright doing an emergency repair
My first customer is always going to be the technicians on the floor to make sure they get what they need. So part of my job is showing our technicians how new technologies and new ideas can not only make their job easier but make their life better.
When you start showing people how data and new technologies can be used to outline the health level of their equipment and improve planning, it doesn’t just affect their quality of life. It affects their family’s quality of life. On Saturday, when someone’s son has a baseball game or he wants to take his son deer hunting over the weekend, he can plan on that and not plan on being called in. My technicians don’t have to answer the phone at two o’clock in the morning anymore.
Also, look at the safety factor of what it’s like to work at night compared to what it’s like to work in planned evolution in daylight. Most of the equipment at manufacturing facilities is stored outside, and it’s usually not very well lit. Anytime you’re forced to work on something at night, you’re having to bring in more lights and more people. It takes longer. Executives don’t want to see downtime.
How have you been able to use Augury’s platform to train your team?
I am grateful to the dashboard we have. We’ve built a lot of our training requirements off of what we found on it. We had to explain to our technicians that an alarm doesn’t mean it was failing right now. The danger means that we probably need to look at it. We had to give guidelines.
Roseburg’s Augury Dashboard
Being able to do that is huge. It was really hard for people to understand that everything’s not an emergency. It’s data, and how you use that data is what really matters. We can make our lives simple with the data or we can make our life miserable if we attack everything.
Has that helped you at all with hiring?
Yes. When we hired a maintenance manager in Simsboro, that was one of the things we sold him on: the fact that we’re not using antiquated technologies. We’re trying to find out what’s out there, what’s new, and we’re willing to invest. We’re willing to invest in new technology in order to improve our quality of life and our product. We absolutely do use it as a selling point and as a retention and recruiting aspect.
Want to learn more? Just reach out and contact us!