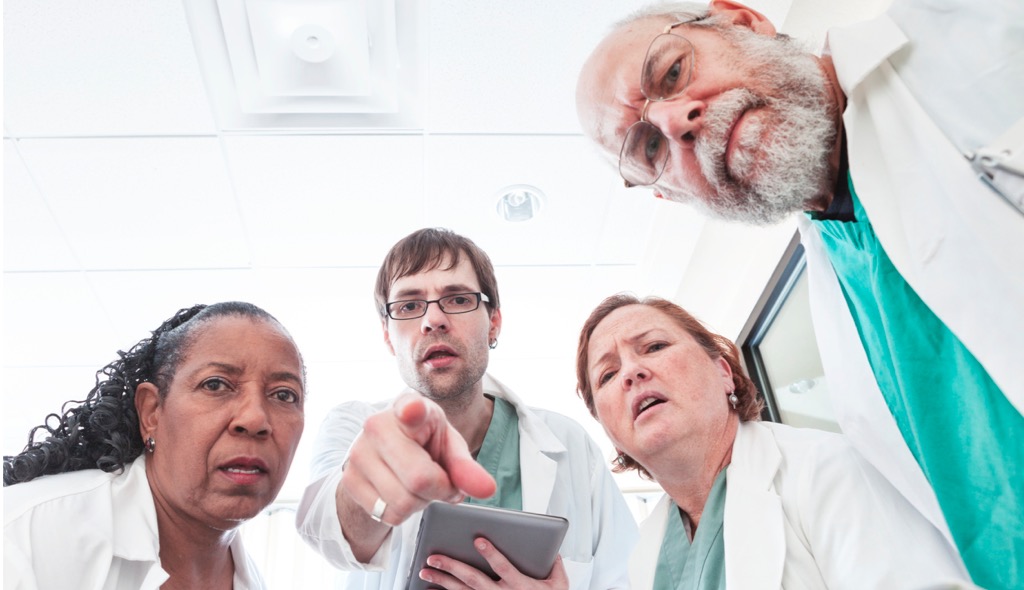
We’re in a perfect storm, and to get the manufacturing industry back on track, some primary issues need to be addressed. In order to reach smoother waters, we need to double-down on: reducing downtime, increasing capacity, optimizing the cost of asset care, and using digital transformation to gain a competitive advantage.
The manufacturing industry has been experiencing growth and change at an extreme rate over the past several years, and problems within the industry have grown alongside it. While the pandemic has certainly exacerbated pain points, the truth is that these issues are tied to long-term trends in the industry.
Consider jobs. According to the U.S. Bureau of Labor Statistics, manufacturing hit its peak workforce numbers in June 1979, with 19.6 million Americans in the industry. It’s been dropping ever since, with the biggest dips occurring during recessions. In June 2019, the bureau reported 12.8 million people were employed in manufacturing, a 35% decrease.
However, worker shortages haven’t led to production losses: Demand has grown, and a trade deficit among U.S. manufacturers has led to increased import dependence.
The combination of a shrinking workforce and consumer demand for more agility has required manufacturers to embrace new ways of thinking and producing.
Consumers have also shifted away from dependence on local manufacturers with the advent of the internet. We have access to a wider range of product options. Supply and demand are not as simple as they once were; they are dynamic and move at lightning speed. There’s been an uptick in product customization, and consumers expect companies to engage in sustainable manufacturing practices. And consumer expectations are higher than ever thanks to online reviews, information sharing, and fierce competition.
The combination of a shrinking workforce and consumer demand for more agility has required manufacturers to embrace new ways of thinking and producing. It accelerated the development and implementation of digital transformation – aka Industry 4.0.
Common industry problems can all be addressed by leveraging predictive technologies already available to manufacturers.
Yet, the number of companies implementing digital strategies dropped more than 40% during the pandemic, hitting numbers closer to those seen in 2017. The two main factors preventing companies from implementing Industry 4.0 practices are revenue and worker shortages, which only serves to highlight just how important digital transformation is in the first place.
Failure to fully implement digital transformation compounds the very issues that it’s meant to solve. Common industry problems – unplanned downtime, need for increased output, high asset-care costs, and gaining an edge over competitors — can all be addressed by leveraging predictive technologies already available to manufacturers.
Pain Point 1: Reduce Unplanned Downtime
Unplanned downtime typically lasts one full day – sometimes more – and has major impacts on production outputs and can add to global supply chain disruptions. While some downtime is necessary for any plant – 100% uptime is a pipe dream, not a goal – unexpected downtime, which is typically caused by machine failures, can cause serious problems.
To reduce downtime in production, best-in-class manufacturing facilities are moving away from reactive strategies and toward preventive strategies using predictive maintenance solutions. Utilizing machine data makes unexpected equipment failure a thing of the past, providing unparalleled supply chain resiliency.
Eliminating unplanned downtime through data-driven predictive maintenance significantly boosts both productivity and employee morale.
And while the financial benefits of reducing unexpected downtime are clear, another high cost of downtime is less talked about: employee morale and workplace satisfaction. Employees being pulled in 10 directions because of the chaotic nature of their facilities aren’t particularly happy or excited about going to work. Thus, eliminating unplanned downtime through data-driven predictive maintenance significantly boosts both productivity and employee morale.
Limiting manufacturing downtime is also important because 81% of companies believe production demand will increase in the coming years, and one-third say decreasing unplanned downtime will determine whether they meet their targets. Predictive maintenance technology can limit downtime and help reach production goals in the following ways:
1) Data-driven insights
Continuously monitoring critical assets provides AI-driven insights into machine performance. This data does more than inform maintenance tasks – it also optimizes routine procedures.
2) Strategically planned maintenance
Real-time machine insights enable you to schedule maintenance when it’s needed. This saves time, money, and energy usually spent on calendar-based strategies.
3) Early notice of potential failures
Predictive maintenance means more notice before a failure occurs. Workers can address issues early, rather than facing problems when they are larger or critical issues. This saves stress and last-minute overtime costs often associated with failing machines.
Pain Point 2: Increase Productivity to Unlock Shadow Capacity
While running a machine at full capacity may seem like the best way to increase production, this isn’t actually the case. Real-time machine insights help manufacturing operations management identify optimal performance settings to balance machine lifecycles with output. High output doesn’t automatically mean high-quality output, so it’s important to have an accurate picture of your machine productivity gap.
The key to stop missing production targets, increasing costs, and losing shelf space is to run machines optimally.
Think of how your revenue can be impacted when a machine doesn’t run optimally: Products in production might not meet quality standards, lack consistency, or become waste. The key to stop missing production targets, increasing costs, and losing shelf space is to run machines optimally.
A condition-based maintenance approach can diagnose mechanical issues that lower quality and yield. This allows you to run machines smarter for longer, enabling you to increase capacity without adding new equipment.
Continuous monitoring of your machines provides accessible, understandable, and actionable insights thanks to these three benefits:
1) 24/7 Monitoring Sees What People Can’t.
Predictive maintenance solutions gather substantial data that workers simply can’t gather on their own and, in turn, reveals problems that might be missed otherwise. And having data on a machine’s historical performance provides information on what issues could evolve into problems in the future.
2) AI Plus 24/7 Machine Monitoring Scales Benefits.
This builds on the last point: Workers cannot gather substantial amounts of data. 24/7 machine monitoring collects a large library of data, and with AI analytics, that information is analyzed and turned into insights that alert teams to machine issues. And when a problem does come up, your team of experts will be able to address it before it impacts your production targets.
3) Increase Your Monitored Assets.
While predictive maintenance usually starts with monitoring critical assets, it doesn’t have to stop there. You can improve machine performance throughout your plant portfolio by monitoring supporting equipment. By doing so, you move from productive critical assets to fully optimized production lines.
Pain Point 3: Optimize Asset Care Costs
Asset care is one of the most expensive aspects of your M&R budget, and these numbers are driven up by fixed preventive maintenance schedules. Parts are often ordered when they’re not needed or purchased when machine problems arise, which can leave you scrambling and paying threefold or even fourfold because of supply chain disruptions or facing down production lines due to long lead times.
There are several stages to optimizing asset care costs, and it’s an organic and ever-evolving process.
Optimizing asset care means finding the balance between those two scenarios — not stocking up on parts you don’t need anytime soon and making sure you have parts on hand when needed.
It’s important to understand that optimization isn’t an overnight process; it depends on how long you’ve been in business and what existing data you have. There are several stages to optimizing asset care costs, and it’s an organic and ever-evolving process.
When you utilize predictive maintenance solutions, you reduce asset costs in the following ways:
1) More efficient labor spending
By eliminating time spent on routine maintenance, you can give your workers that time to focus on higher-level work and save money on unexpected overtime.
2) Fewer machine failures
With calendar-based maintenance, issues may slip through the cracks, damaging production output or even leading to asset failure. Predictive maintenance saves manufacturers the costs associated with unplanned downtime, which averages $260,000 per hour
3) Improved inventory management
Besides the cost of acquiring and storing parts, letting them sit on the shelf is a tax liability. Of course, not having those parts when you need them costs thousands in lost productivity and expedited fees. Continuous monitoring and real-time machine health insights allow you to predict how much inventory is needed and when in order to improve your M&R budget.
Pain Point 4: The Competitive Advantage of Digital Transformation
The pandemic and subsequent supply chain disruptions have highlighted how vital it is for manufacturers to embrace digital transformation strategies for a competitive advantage.
There will always be supply chain disruptions, but having a proactive strategy in place will help you rise above those inevitable challenges. Embracing Industry 4.0’s mantra of leveraging manufacturing technology insights is the best way to do that.
By digitizing your maintenance practices, you’ll gain quick machine insights and fast ROI.
It’s predicted that by 2025, spending on digital transformation in the manufacturing industry will be more than $816 billion, and 90% of leaders within the industry currently recognize its value.
By digitizing your maintenance practices, you’ll gain quick machine insights and fast ROI. The success of digital solutions is made possible because of the following:
1) Makes Space for Strategic Initiatives With Remote Management
With fewer people on-site than ever before, remote management tools are essential for team collaboration. Managers can pull machine insights from machine health data on their phones or computers, enabling them to address situations and communicate with teams wherever they are.
2) Upskills Workers With Digital Tools
AI-driven machine health monitoring provides teams with new insights and capabilities. With fewer machines running to failure, teams can focus on higher-value work that can unlock better processes and transform roles. In some cases, companies have created new positions to focus on their digital initiatives.
3) Creates a Culture of Collaboration and Accountability
Collaboration across your entire organization can quickly scale your digital transformation efforts. Encourage regular conversations around machine health, highlight machine wins, and share best practices with other teams and sites. Machine health monitoring platforms enable better cross-departmental communication, connecting different stakeholders with the data they need to transform operations and inform future production decisions.
Addressing any of these pain points with predictive solutions will help you meet production goals and put you ahead of competitors. Supply chain disruptions and labor issues aren’t going away anytime soon, but improving your machine performance is within your control, and doing so will improve your supply chain resiliency.|
To start eliminating unplanned downtime, increasing capacity, optimizing care costs, and gaining an edge over competitors, contact Augury for your demo.