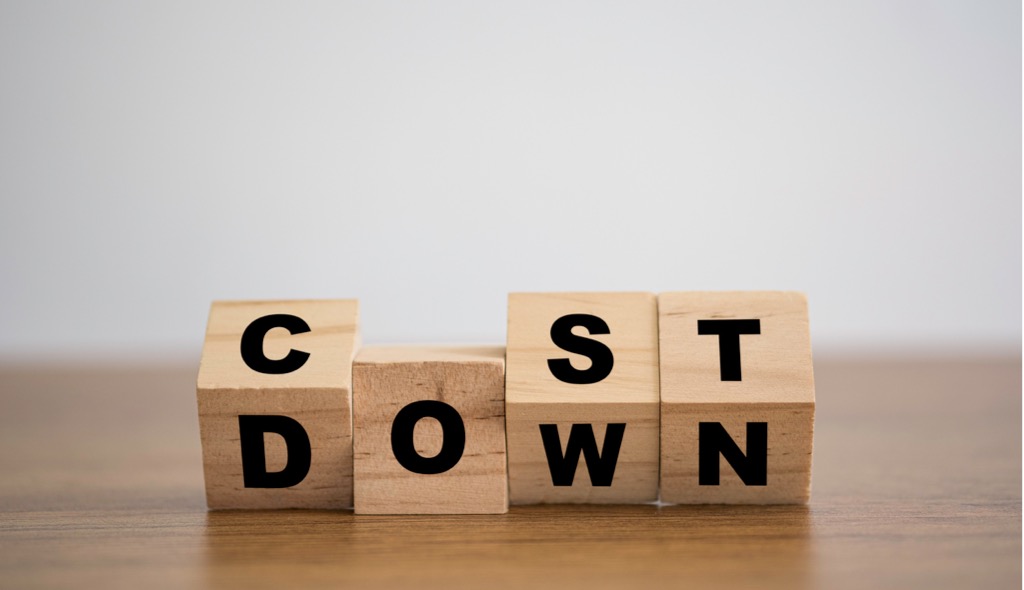
Manufacturing costs are on the rise across industries. Meanwhile, many factors contributing to higher expenses are out of a manufacturer’s control. One thing that does remain within your grasp? Production costs. You can drive down production-related expenses such as waste, parts, and downtime by monitoring and responding to machine health in real time.
According to a recent survey by McKinsey, 63% of CPG companies reported a year-over-year increase in manufacturing costs of anywhere from 5% to 20% in 2020. With little control over the costs of raw materials, manufacturing companies in every sector are left with a question of how to reduce production costs in manufacturing by other means.
While manufacturers can certainly try their hand at negotiating with suppliers, the answer may be closer to operations than one might think: machine maintenance and reliability. Thanks to the arrival of AI-driven machine health platforms, like Augury, additional costs associated with repairs can be effectively mitigated if not eliminated by having deep insights into when machines are going to fail and where specifically that failure will take place.
See how Augury’s machine health monitoring
platform works.
The following are just a few ways Augury’s machine health monitoring platform can help drive down expenses:
1) Predictive Parts Replacement
Traditionally, manufacturers have taken a more reactive than proactive approach to parts replacements and repairs. And when they can’t see a problem coming, they can easily wind up in the unfortunate position of expediting parts shipments. This can increase costs exponentially. In fact, I’ve even had to buy an $8,000 flight just to fly a $1,500 machine part from Germany to avoid an issue for a manufacturer that could have been avoided with machine health monitoring.
With Augury’s machine health monitoring system – made up of machine sensors and AI algorithms to glean insights from machine health data – manufacturers can predict when a machine will need a specific part. They can then take necessary measures to obtain it without incurring additional costs for expediting the process.
What’s more, the machine health data from Augury’s platform is easy to export and share. Therefore, it could be sent to off-site experts who could then walk technicians through tricky repair processes virtually. Instead of paying to fly experts in, you can access them from anywhere in the world at any time.
2) Reducing Waste
Many industries, such as CPG and Pharma, rely on manufacturing through batch production. If a machine failure were to occur during batch production, the manufacturing company would lose an entire batch of goods. For example, say a potato chip company mixes batches of potato chips, but a mixer goes out in the middle of production. The mixer must be replaced, and the entire batch of chips goes to waste. And as waste goes up, so do costs.
With machine health data and insights, however, the manufacturer would know beforehand that the mixer was in poor condition. They could replace the part before putting in the batch, saving themselves from wasting a lot of product.
3) Right-Sizing Storerooms
Many manufacturers still rely too heavily on calendar-based preventive maintenance methods, where equipment care is set at regular intervals according to time or usage. Scheduling this way, however, leaves storerooms stocked with excess parts and pieces, wasting valuable space and driving up costs. Basing maintenance on time or usage can also lead to late or missed maintenance, which could result in costly repairs.
With a data-based machine health monitoring system and meter-based PM schedule instead, manufacturers can know exactly when to repair or replace parts. The approach also offers a fuller understanding of the health and life cycle of equipment. This, in turn, slows down the rate of parts consumption, eliminates the need for excess inventory, and reduces the chances of unplanned downtime. Meanwhile, costs are saved throughout the process.
4) Eliminating Unplanned Downtime
On average, manufacturers experience a loss of $260,000 per hour of unplanned machine downtime. Worse yet, 82% of manufacturers run into the problem at least once a year. As indicated earlier, machine health monitoring through data-based systems can make manufacturers aware of the signs that equipment is on the verge of breaking down.
With those insights, manufacturers can plan scheduled shutdowns for machine repairs. And predictive diagnostics and repair insights from Augury’s platform can mean shorter, more efficient planned downtime events. That way, machines get up and running faster, back to producing and generating revenue.
Manufacturing almost any product can be expensive. The costs of raw materials alone are cutting into the profit margins for many manufacturers. And while reducing per-unit costs can come in a variety of forms, the one option under manufacturers’ full control is machine maintenance.
To learn more about how Augury’s platform provides AI-driven machine health monitoring that can reduce your production costs, get in touch today.